Pressmeddelande -
Innovation Lab: at Agritechnica 2023 CLAAS will be demonstrating sustainable and autonomous technology for today's agriculture and beyond
With a new stand concept and a host of new products, CLAAS intends to engage in forward-thinking dialogue with customers at this year’s Agritechnica. New products will be presented in Innovation Alley at the stand's centre, while the new Innovation Lab will showcase highly automated and autonomous sustainable future farming.
With an innovative stand concept and a modernised, even more customer-friendly tradeshow presence, CLAAS is breaking new ground at this year’s Agritechnica – the world’s leading agricultural machinery show. Visitors to the 5800 m2 stand will not only be greeted by familiar CLAAS products and innovations such as the EVION, the DISCO 9700 series and the XERION 12 Series. For the first time, they will also get a comprehensive behind-the-scenes glimpse of development projects in the fields of cab/HMI, autonomy and alternative drives. At the Innovation Lab on the CLAAS stand in Hall 13, interested farmers, contractors, students and apprentices will be able to experience different future technologies at close hand and discuss them with CLAAS staff – here, innovation meets interaction, discussion and feedback. Some of the studies and projects on display will be ready for series production in the short- to medium-term and have already secured a silver Agritechnica Innovation Award. Others are geared towards a more long-term perspective.
Autonomous XERION demonstrator: large tractor for highly automated and autonomous fieldwork
CLAAS will be unveiling a prototype autonomous large tractor at Agritechnica 2023. A XERION 12.590 TERRA TRAC has been equipped with relevant sensors such as LIDAR and camera systems, as well as other technology for track planning and process monitoring. Other vehicles are already undergoing further research and component testing in the field.
High-level automation and autonomy are key globally relevant themes for numerous agricultural applications. CLAAS is developing technologies for autonomous field cultivation independently and in partnerships such as 3A – ADVANCED AUTOMATION & AUTONOMY. Practical fieldwork such as tillage with large tractors is just one of the applications scenarios being prioritised. “Large tractors equipped for highly automated and autonomous work are mainly of interest to farms that cannot make full use of a conventional AgBot or whose machine and implement fleet does not match the AgBot’s performance characteristics", explains Christoph Molitor, Head of Technology Management at CLAAS. "In addition to the general shortage of skilled workers in agriculture, we see weather-related harvest delays and mechanical crop care as factors that lead to a concentrated need for labor or a high demand for work capacity. High automation and autonomy can help to equalize such work peaks and labor-intensive agricultural processes."

CLAAS will be unveiling the XERION 12.590 TERRA TRAC in the Innovation Lab – a demonstration machine for highly automated and autonomous cultivation with Autonomy connect Co-Pilot and Auto-Pilot.
The XERION 12.590 TERRA TRAC with Autonomy connect on display in the Innovation Lab is technically set up for high automation (Autonomy connect Co-Pilot) and autonomy (Autonomy connect Auto-Pilot). Co-Pilot provides the highest level of process automation, including planning with Autonomy connect – which can be fully integrated into the CLAAS connect platform. With Co-Pilot, the operator mainly performs a supervisory role, while preplanned tractor and implement functions and settings are performed fully automatically by the tractor-implement combination. As before, the operator can intervene directly in the process and further optimise it from the cab. With Auto-Pilot, the tractor operates fully autonomously with no one in the cab. Tasks are planned exactly as with Co-Pilot, but the tractor is equipped with enhanced environment recognition technology in addition to LIDAR, including special camera systems, further safety technology and automated braking. Once on the market, the Autonomy connect planning tool can be fully integrated into the CLAAS connect Internet portal, making it easy to use for day-to-day operations without needing an additional portal.
The Amazone Cenius cultivator also on display in the Innovation Lab is equipped with Amazone AutoTill technology for highly automated and autonomous work. This technology monitors the working position, working depth and roller speed as well as detecting share loss and clogging in the tine area. Data recorded by the cultivator are compared with tractor data, enabling the operating speed to be reduced when blockages are detected or the cultivator raised when roller slip is too high.
AgXeed, thermalDRONES and CLAAS Saulgau combine highly automated and autonomous mowing with wildlife rescue
Drones with thermal imaging cameras are now a practical, reliable and effective means of detecting wildlife such as roe deer fawns and ground-nesting birds shortly before mowing grassland or whole-crop silage. The system generally scans the live image for a heat source. When one is detected, the search is interrupted to allow helpers to move animals to safety or mark their location or nest site.
CLAAS, thermal DRONES and AgXeed have pooled their expertise to develop a common drone interface for autonomous mowing. Data on heat sources identified during the drone flight are initially saved then processed with KI software and transferred to the process planning tool, along with relevant GPS positioning data. This tool integrates the data into the route planning system, enabling the autonomous mowing equipment to be safely steered around the wildlife locations. This rerouting is particularly useful in cases where ground-nesting birds are protected and therefore cannot be removed. Farmers and contractors can track the machine’s route live on their smartphone, tablet or PC via the AgXeed portal. The use of autonomous mower combinations thus meets the combined needs for high area outputs and wildlife-friendly grassland management. Furthermore, it enables farmers to comply with reporting requirements by providing documentary evidence of measures taken before mowing.

Schematic representation of the data routes for automated and autonomous mowing after drone scanning.
But it's not just autonomous field robots that can benefit from this technology. It can also be used with autonomous tractors and highly automated tractors and harvesting machines steered along pre-planned routes by the operator – making it an attractive solution for customers today. The system ensures that POI data on wildlife locations is collected only within known, previously specified field boundaries. Farmers can transfer field boundaries from their farm management system. Alternatively, if these data are not available, the drone pilot can mark the field boundaries themselves on their screen.
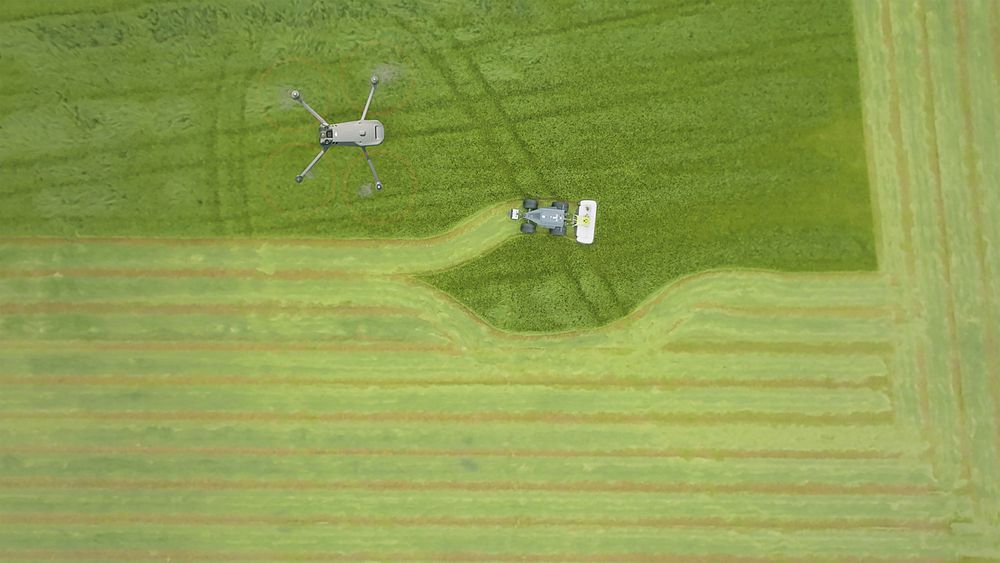
The drone interface allows autonomous field robots and tractors to steer around nests and wildlife located before mowing using thermalDRONES technology.
Battery-electric SCORPION 732e: Telehandler prototype for locally emission-free and quiet materials handling
When it comes to developing alternative drives, CLAAS takes an open-minded approach with a strong customer focus. In the medium term, combustion engines running on sustainable fuels such as HVO (hydrotreated vegetable oils) are superior to other concepts in the upper performance range in terms of energy density and tank infrastructure. However, battery-electric, locally emission-free drives offer significant potential in the lower performance range and for applications such as materials handling, yard work and municipal use.
Telehandlers are versatile machines for precision-lifting heavy loads, loading trailers or anaerobic digesters and stacking bales. A battery-electric telehandler like the CLAAS SCORPION 732e – a joint development with Liebherr – offers many advantages: the machine is very quiet and locally emission-free, which is particularly beneficial for people and livestock during indoor work. Two independent 90 kW electric drives, a modular 64 kWh battery concept for up to 4 hours' use and a 22 kW on-board battery charger ensure ample performance and flexibility. It offers maximum tractive power of 53 kN and a top speed of 30 km/h. Furthermore, farmers can charge the battery using electricity generated from their on-farm PV system or biogas plant.

The prototype SCORPION 732e has a range of up to four hours. With the 22 kW on-board charger, farmers can charge the battery using electricity generated from their own PV system or biogas plant.
Semi-electric combine harvester: a concept for homogenous engine loading and reduced fuel consumption
Combine harvesters often face a mix of operating conditions during harvesting. Inconsistent grain and straw yields, volunteers or uneven terrain mean that drives and power units are constantly having to adjust to achieve the best possible overall performance – high productivity, high harvest quality and high efficiency. Continuously high drive utilisation without major speed fluctuations and ultra-homogenous crop flow is desirable not only in terms of efficiency but also to ensure optimal separation and cleaning performance. But this is very difficult to achieve in heterogeneous crop stands.
A semi-electric drive on the combine harvester – developed by CLAAS and tested in the field – can help flatten load peaks and significantly increase efficiency. When harvesting conditions are straightforward, engine power not needed for the combine harvester drive is converted to electrical energy via a generator and stored in the battery. When harvesting conditions become difficult, for instance in high-yield areas or when discharging on the move, the electric motor steps in to support the mechanical drive using stored electrical energy from the battery, replacing a conventional ‘boost’ produced by the engine performance characteristics. This enables load peaks to be bridged for several seconds, and with automatic load distribution, the combine harvester can consistently operate in the optimum performance range.
This concept enables a smaller, less powerful combustion engine with an output of around 400 kW to be operated in the low-speed range at 1600 instead of 1800 rpm thanks to the additional 40 kW electric motor and 3 kWh battery with 48 V inverter. In field trials, this semi-electric hybrid concept reduced fuel consumption by up to 10 per cent.
Since the electric drive operates in the low-voltage range (< 60V touch voltage), it does not require the complex safety precautions associated with higher-voltage drives. Maintenance can be carried out without further safety measures or special training.
Cab 4.0 and Cab10Future: a window into the future operator environment on harvesting machines and tractors
Operators are already supported by numerous automatic assistance systems designed to maximise the potential of complex harvesting machines, and the degree of automation is set to increase in the next few years. As a result, there will be periods when operators have so little to do – even in terms of supervision – that they will feel underworked and tire quickly. So in future, harvesting machine cabs must enable operators to perform other activities in addition to those relating specifically to the machine.
The ‘Cab 4.0 – OnField’ research project uses the latest technology such as joystick steering, operator fitness detection and eye tracking to show what the future workplace might look like. This concept features innovative cab equipment with Internet connection and different human-machine interfaces such as cameras, head-up displays, monitors, keypads and much more. With this equipment it is possible to continuously monitor the operator's occupation level and thus establish two-way communication. When operators are underworked, the system suggests alternative tasks and activities for them to do.
The core element is a virtual assistant supported by an eye tracker in the roof, which speaks to the operator when signs of fatigue are detected and recommends appropriate action. At the press of the button, the operator can adjust the seat to three positions to carry out these actions. The seat faces forward in ‘work mode’ but can be swivelled to the left for ‘relaxation mode’. In this position, the operator can perform light gymnastic exercises to re-energise their bodies. Alternatively, on the head-up display they can find information about relaxation and stress relief, watch tutorials or do personal work.
In ‘office mode’ the seat is swivelled to the right so the operator can see the head-up display on the right-hand window. In this position, they can place a portable keypad tablet with trackpad between the armrests to do office work such as emails, Internet research, or planning, documentation and controlling work in the farm management system. Farm managers currently have to spend additional time in the office on these tasks, restricting their free time.
The harvesting machine must be equipped with automatic front-area monitoring for the new Cab 4.0 functions to work effectively in the field. The operator is notified in good time of any obstacle detected by the front-area monitoring system so that they can return to work mode and supervise the steering of the machine.
Five companies and institutions are involved in developing the Cab 4.0: Karlsruhe Institute of Technology (Institute of Human and Industrial Engineering and Institute of Mobile Machines), Institute of Agricultural Engineering at the University of Hohenheim, InMach Intelligente Maschinen GmbH, Budde Industrie Design GmbH and Claas Selbstfahrende Erntemaschinen GmbH. The Cab 4.0 project was funded by the Federal Ministry of Education and Research (BMBF) in line with ‘Agricultural systems of the future’ funding guidelines. Focus group workshops with operators and farm managers indicate a high level of user acceptance for the project, which was launched in 2019.

Cab10Future is the long-term CLAAS vision of a cab for tractors and harvesting machines. Large displays, impressive all-round visibility as well as recyclable and high-quality materials characterize the interior of the Cab10Future.
CLAAS unveils its own vision of the future cab with CAB10Future: more comfortable workspace with a seat that rotates by up to 60 degrees in both directions for close-up work; intelligent lighting for a more relaxed working environment; large screens in the front focus area for full-on digitisation; and sustainable construction with easily replaceable wear-prone modules and use of recycled materials. ‘Transparent’ A-pillars with cameras and displays reflecting the environment and the absence of a steering column (autonomous operation) create an impressive spatial experience for the operator. 360° exterior lighting simplifies external machine communication.
Ämnen
Kategorier
Swedish Agro
Swedish Agro är ett svenskt företag som förser lantbrukare med insatsvaror, foder och maskiner av högsta kvalitet. Företaget representerar CLAAS, HORSCH, METSJÖ, RAUCH, SPEARHEAD, SCANSTONE, AVR, AGXEED och DALBO i Sverige. Service och reservdelar finns mobilt och på 24 orter både via egna anläggningar och servicepartners. Med en av Europas modernaste foderfabriker tillverkas foder för flera djurslag. Swedish Agro är ett företag i Danish Agro-koncernen som består av en rad företag inom lantbruksbranschen i norra Europa.