Nyhet -
Paper Province Summit – tillsammans med stålindustrin
Under Processteknikmässan i Göteborg arrangerade Paper Province en konferens i samarbete med Sustainable Steel Region. Således en samverkan mellan ett gammalt och ett nytt nätverk. Temat var industrierna resiliens, med andra ord hur de ökar sin säkerhet avseende produktionsstörningar och skapar trygga leveranskedjor.
AV KJELL-ARNE LARSSON
Konferensen kom att handla om allt från att producera sin egen el, till att klara underhåll och reparationer av sina tillverkningsresurser. Ett par tunga inslag tog upp möjligheterna att, med hjälp av 3D-printning ta fram egna komponenter och reservdelar. Att miljön och klimatet samtidigt ska värnas, glömdes heller inte bort. Utan en fungerande natur och jord, finns det ingen bas för att utveckla varken verksamhet eller affärer.
ABB visar möjligheterna i industrins omställning
De första talarna presenterade, betecknande nog för konferensen, ett case från skogsindustrin och ett från stålindustrin. Martin Björnmalm, Local Business Line Manager Pulp & Paper och Metals i Sverige, och Per-Inge Bengtsson, Global Business Driver, Plant Electrification Pulp & Paper, båda från ABB, berättade vad de kan göra för att industrin ska hushålla med energi och bli mer hållbar.
ABB levererar som bekant många typer av maskiner (elektriska och mekaniska) för verkstads- och processindustrin samt för energisektorn. Dessutom styrsystem som 800XA, QCS med mera.
ABB har en hållbarhetsagenda med tre fokusområden: möjliggöra klimatneutralitet 2050, genom cirkularitet och effektivitet få ner resursförbrukningen, samt utveckla den sociala hållbarheten. Under konferensen visades två exempel där ABB haft betydande roller i att hjälpa kunden att uppnå bland annat bättre energieffektivitet. Metsä Fibre i Finland har byggt norra halvklotets största massafabrik, som årligen tillverkar 1,5 miljoner ton massa. ABB har levererat all elektrifiering och drivteknik; från elmotorer, till skyddsreläer, säkerhetsbrytare, frekvensomriktare, transformatorer, elektrifierings- och drivteknik samt styrsystem för motorer och tillståndsövervakning med fjärrsupport. Dessutom hjälpte ABB Metsä att skriva förfrågningsunderlag för att upphandla en fabrik som klarar sig helt utan fossila bränslen.
Det andra exemplet rörde ett stålverk hos JSW Dolvi i Indien. Fabrikens meltshop, där smältan får sin slutliga sammansättning genom tillsatser, förbrukade onödigt mycket energi när smältan behövdes värmas om. Genom bättre mätning, styrning och optimering kunde energieffektiviteten förbättras. Produktiviteten ökade tack vare
4–5 procent högre gjuthastighet genom bättre anpassning av smältans temperatur. Minskade tappningsfördröjningar i Electric Arc Furnace eller konvertrar tack vare effektivare tidsplanering av kranar för skänkrörelser. Dessutom bättre skänkhantering och underhållsplanering tack vare tillgång till historiska data över alla rörelser. Det blev också ökad arbetskraftsproduktivitet eftersom manuella ingrepp eller kvitteringar inte behövs.
Martin Björnmalm och Per-Inge Bengtsson pekade avslutningsvis på att samarbete i hela värdekedjan och tidiga insatser i projekt ger bra förutsättningar för kostnadseffektiva och framtidssäkrade lösningar.
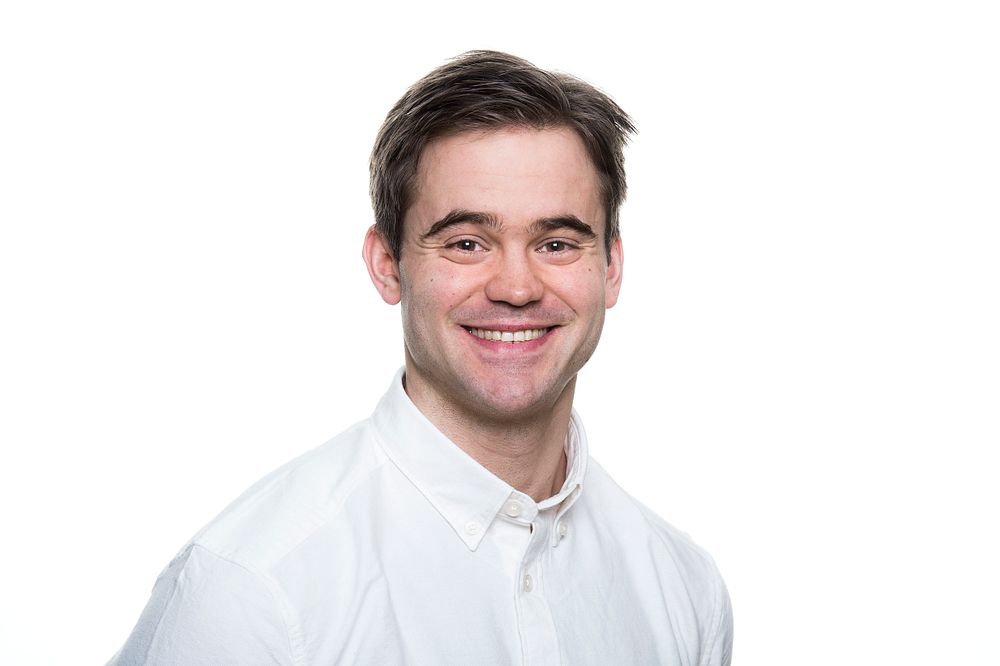
ABB:s Martin Björnmalm, Local Business Line Manager Pulp & Paper och Metals, berättade vad de kan göra för att industrin ska hushålla med energi och bli mer hållbar. Bild: ABB
Restströmmar – från spill till värdefull resurs
Lars Birging från Zigrid berättade om företagets koncept för att omvandla lågtempererad spillvärme till el som används lokalt.
– Det finns enormt mycket restvärme i industrin. Bara en tredjedel av energin används till något nyttigt. Vi kan ta vara på flöden i låga temperaturer ned till 50 grader, berättar Lars Birging.
Spillvärme finns i stålverk, kärnkraftverk, kyltorn och datacenter. Flera andra värmekällor kan bli aktuella såsom vätgasanläggningar, rökgaskondenseringar och CCS-anläggningar.
Zigrid har utvecklat en utrustning som tar vara på lågvärdig värme, "växlar över den" i en unik metod, utan en traditionell turbin, till mekaniska energi som driver en elgenerator. En pilot testas nu i ett gjuteri i Guldsmedshyttan. Zigrid får stöd från ett EU-projekt, där resultatet ska redovisas 2026. Koldioxidutsläppet från processen är beräknat till under 5 gram/kWh, vilket är extremt mycket lägre än vid fossil elproduktion.
Förnybar energi och flexibilitet i en energiintensiv industri
Anna Boss som är energispecialist hos Rottneros berättade om företagets investering i solcellspark och batterilager. Företagets huvudanläggningar är massafabrikerna i Vallvik (kemisk massa) och Rottneros (mekanisk massa). Den senare är den mest elintensiva och det är där investeringar har gjorts.
– Vi såg höga elpriser och ville minska beroendet av köpt energi, säger Anna Boss.
Solparken har uppförts på ett 3,2 ha stort deponiområde intill fabriken. Det är en sluttäckt yta. Förankring kunde inte utföras med pålning eftersom tätskiktet då skulle skadas. Solcellspanelerna med sina stativ hålls därför på plats med tyngder. Anläggningen har 4284 paneler med sammanlagda effekten 2,7 MW (paneleffekt, 1,6 MW efter växelriktare). Under två veckor i full drift producerades 67 MWh.
Batterilagret har inte byggts för att lagra energi för egen del, eftersom fabriken har elbehov dygnet runt och man dessutom inte har avtal för att leverera el till nätet. I stället är inriktningen i första hand att sälja stödtjänster till Svenska Kraftnät. Tjänsterna är framförallt FCR-D, FCR-N, FFR och mFRR. Batterilagret har kapaciteten 8,9 MWh.
– Hela projektet har varit utmanande, men nu står vi bättre rustade och fortsätter samtidigt med andra energiprojekt, avslutar Anna Boss.
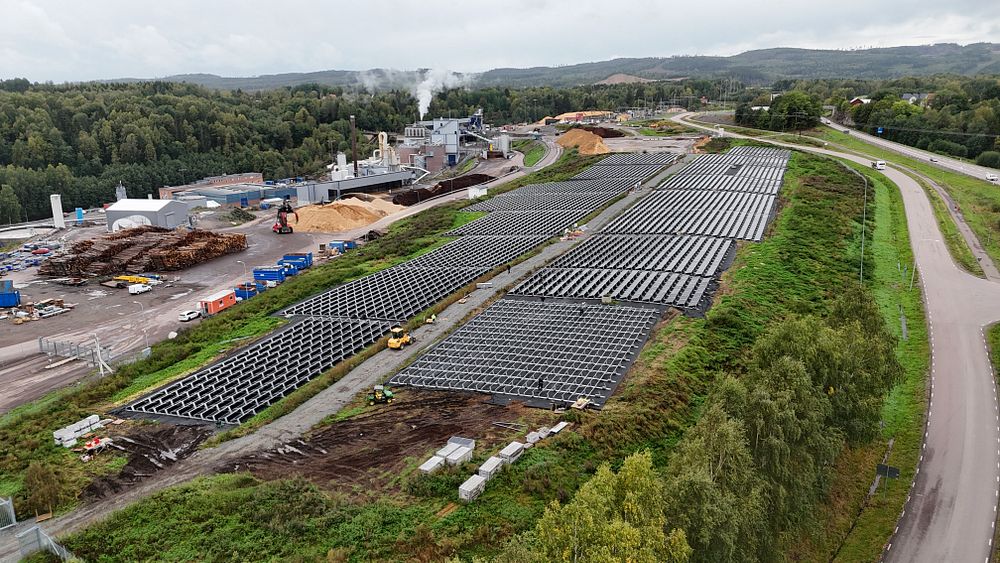
Solparken har uppförts på ett 3,2 ha stort deponiområde intill Rottneros fabrik. Det är en sluttäckt yta. Förankring kunde inte utföras med pålning eftersom tätskiktet då skulle skadas. I stället användes tyngder på stativen.
Framtidens gröna stål – hur funkar det?
GreenIron är ett företag som startade 2018, och som utvecklar teknik för fossilfri metallframställning, bland annat genom att återvinna biflöden från stål- och gruvindustrin. Restprodukter i form av oxider går att återvinna genom att reducera dem med vätgas, och där vatten blir enda restprodukt. Det är en patenterad teknik, i en unik batch-process, som koncept för att driva koldioxidfri tillverkning och minska industrins utsläpp.
– Vår teknik bidrar till att stålverk och gjuterier kan bli mer cirkulära. Vartenda gram som idag läggs på deponi ska kunna återvinnas i stället, säger Tanja Ilic, chief commercial officer hos GreenIron.
De viktigaste restprodukterna är filterstoft, glödskal och slagg. Innehållet består av metaller som har oxiderats. Det kan röra sig om järn, koppar, magnesium, nickel med flera metaller. Restprodukter kan komma från stålverk, gjuterier, valsverk och tillverkningsindustri. Även från energianläggningar, och då rör det sig om olika askor.
GreenIrons process är i huvudsak en reduktion. Oxiderna reduceras med vätgas i en reduktionsugn, och produkten blir järnsvamp (om det är järn som återvinns) och vatten. Det uppstår 500 liter vatten per ton metall.
Företaget har testkört med gott resultat fler än 120 olika material i en demo- och testugn i Kumla. I år byggs en fullskalig ugn i Sandviken. Den får en kapacitet på 5 ton per timme. Lite kan tyckas, men det är bättre att börja någonstans än att inte göra något alls.
En GreenIron-anläggning kan sättas upp på cirka 9 månader. Företag som tar vara på möjligheten, kan minska sina inköpskostnader för material med cirka 5–10 procent genom att återvinna restprodukter. Det blir möjligt att på motsvarande sätt återvinna många andra metaller såsom legeringsmetallerna krom och molybden.
– För att lyckas med omställningen till ett hållbart samhälle, kan vi inte applicera metoderna vi lärde oss i skolan. Vi måste använda helt nya metoder och det krävs samarbete. Här kommer framtidens gröna stål att bli viktigt, avslutade Tanja Ilic.
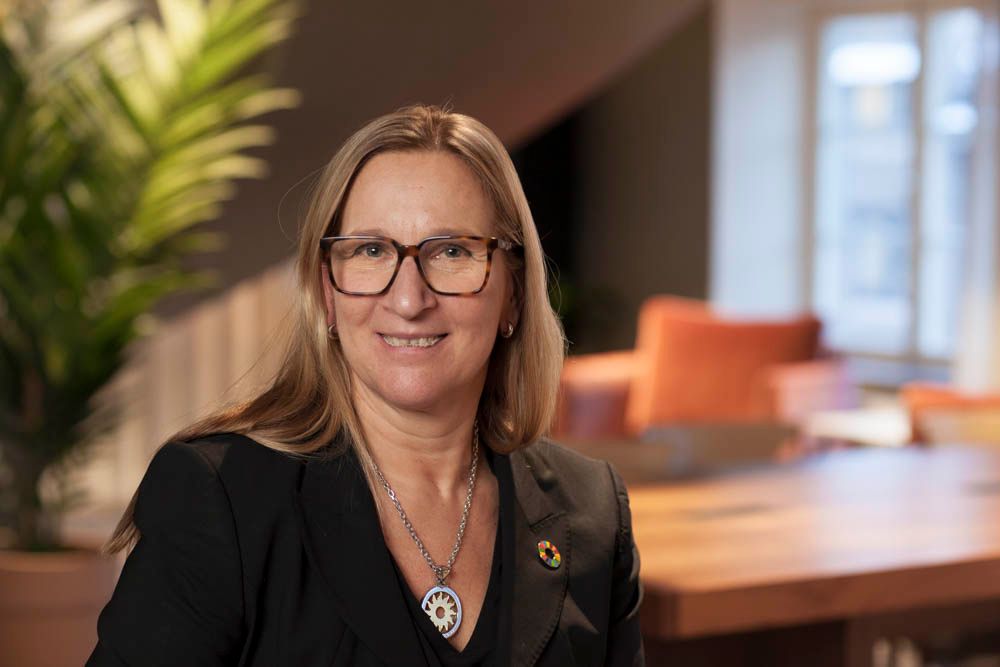
– Vår teknik bidrar till att stålverk och gjuterier kan bli mer cirkulära. Vartenda gram som idag läggs på deponi ska kunna återvinnas i stället, säger Tanja Ilic, chief commercial officer hos GreenIron. Bild: Mikael Dubois
Cirkulärt material – ett lönsamt komplement till att handla nytt
Visibla är ett företag som gynnar cirkulär handel för verkstadsindustrin. En typisk verkstad får spillbitar och helbitar över av stål, koppar och andra material. Förhoppningen är oftast att de ska komma till användning i samma företag i ett senare projekt. Material blir emellertid ofta liggande i flera år, utan att någon bryr sig. Ingen vet vad eller hur mycket som finns lagrat. Kanske verkstaden då ska sätta en tidsbegränsning. Sådant som inte har använts borde då säljas. Men svårt och tidsödande att klara hela affären själv. Då går det att ta hjälp av Visibla, som nästan är som Blocket, men för verkstadsindustrin.
Material som flödar på andrahandsmarknaden är billigare än nytt, men dyrare än skrotvärdet. Om marknaden tack vare Visibla och andra aktörer kan växa, då görs affärer som alla involverade aktörer tjänar på. Dessutom tjänar naturen på denna ökade cirkularitet.
Kritiska reservdelar – snabb produktion lokalt
Det norska företaget Ivaldi är inriktat på ODM – On Demand Manufacturing – att tillverka komponenter och reservdelar inom kort – helst lokalt – efter kundens beställning. Därmed förkortas leverantörskedjorna. Företaget använder främst 3D-printning. Man var först i världen med 3D-printade delar inom marina sektorn och först med ett kommersiellt 3D-print-erbjudande inom gruvdrift.
Konceptet går ut på att i stället för att skicka komponenter och reservdelar långa sträckor skickas digitala ritningar. Efter kundens order går den till Ivaldis närmaste produktionsenhet, vilken fungerar som ett digitalt lager. Delen tillverkas i ett Local Manufacturing Center, som tillhör Ivaldi eller är fristående.
För On Demand Manufacturing kan även andra tekniker användas, som laser, UV-ljus och smältning.
Fördelarna med ODM är givetvis besparingar i transporter och kostnader. Mängden avfall och överskott minskar, liksom klimatbelastningen. Anläggningsägaren behöver inte själv lägga massor av reservdelar på eget lager, som kanske så småningom delvis skrotas. ODM kan också skapa fler arbetstillfällen lokalt. Konceptet bidrar till att förbättra resiliensen hos företaget, vilket var temat för dagens Paper Province Summit.
– Vi bör också tänka på att hela produkter kan tillverkas av 3D-printade komponenter och att det går att producera även med andra on-demand-verktyg, berättade företagets vd Espen Sivertsen och visade foton på självkörande bussar och andra produkter. 3D-print i sig själv är begränsat, men kombinerat med andra on-demand-produktionsrobotar blir det mer kostnadseffektivt och implementerbart.
Och när det handlar om reservdelar kan en ny sådan vara bättre än originalet, vilket kan göra att din maskin blir bättre steg för steg.
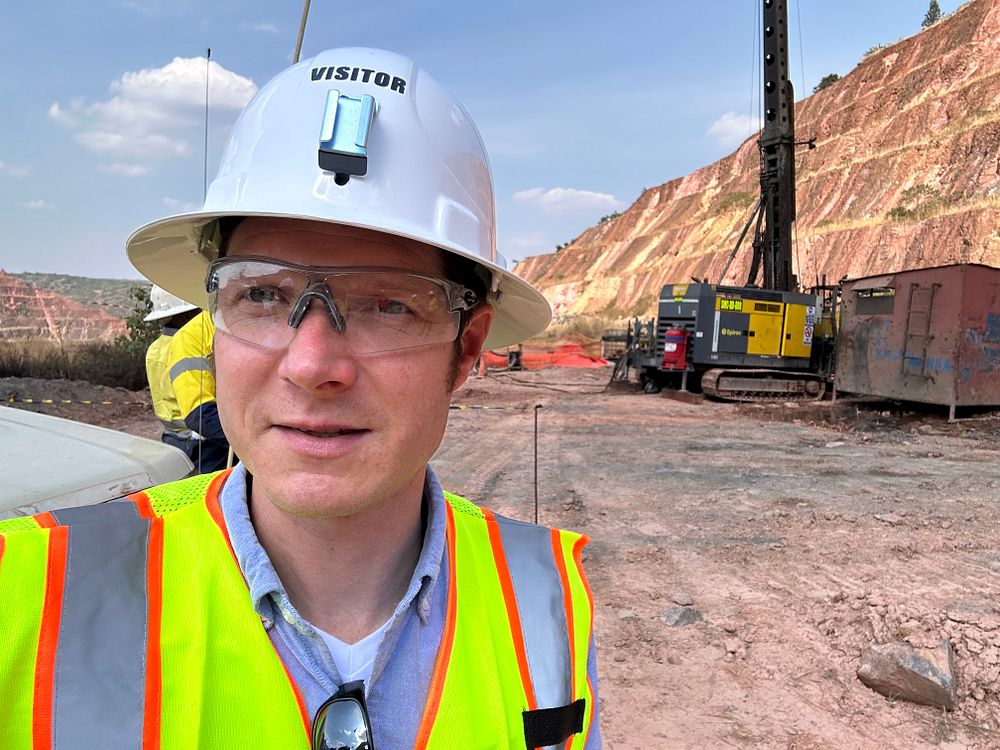
– 3D-print i sig själv är begränsat, men kombinerat med andra on-demand-produktionsrobotar blir det mer kostnadseffektivt och implementerbart, säger Ivaldis vd Espen Sivertsen.
Stora detaljer
Ivaldi visade en rad exempel på komponenter som går att 3D-printa. Men är det möjligt att tillverka även stora ståldetaljer som väger flera ton? Ja, uppenbarligen kan det bli det, för tekniken visades i en presentation från SAAM. Förkortningen står för Submerged Arc Additive Manufacturing.
För att kunna printa stora detaljer måste printningen gå snabbt. Laser DED klarar 2–8 kg/tim och WAAM 2–10 kg/tim. SAAM ska klara från ungefär 25 till 100 kg/tim.
(Laser DED är Laser Directed Energy Deposition, WAAM är Wire Arc Additive Manufacturing som baseras på MIG, TIG eller plasmasvets.)
– Om man kan printa med 100 kilo i timmen går det att konkurrera med gjutning, berättade Magnus Brännbacka, som är vd för SAAM AB.
Principen baseras på svetsning med tråd under ett pulver som bildar slagg och skyddar ljusbågen. Fördelarna är många:
• Kan ersätta smide eller gjutning
• Kort leveranstid
• Mycket högt utbyte, dvs. litet spill
• Goda materialegenskaper, bättre än smide
• Homogent
• Jämna egenskaper över stora dimensioner
• Möjligt att variera material och materialegenskaper i samma komponent
• Går att legera i smältbadet med hjälp av flera trådar
• Egen tråd under framtagning (maråldring)
Företaget är redan igång med printning i sin anläggning i Kristinehamn. Där har man också tillgång till ett labb som testar framtagna delar.
– Materialegenskaperna visar fantastiskt goda resultat och hållfasthetsvärdena är bra med en mycket hög brottseghet. Om vi kan printa snabbt, kan vi också printa stort, ifall vi klarar att behålla egenskaperna hela vägen.
Tekniken öppnar också för andra tillämpningar, som att lägga på ett slitskikt, att komplettera en detalj (t.ex. med en fläns på ett rör) och ge olika delar av en komponent olika egenskaper genom att välja svetstrådar, exempelvis skapa en seg kärna och en slitstark yta.
– Vårt mål är att etablera printcentraler på fem orter landet runt, avslöjar Magnus Brännbacka.
Som för övrig berättar att processen går att sätta upp i en container, där utrustningen hanteras av en enda operatör.
Var det bättre förr? Från slit-och-släng till bevarande
Under den rubriken talade och filosoferade Anders Andersson från Fagerberg och Richard Denlin från Indutrade, en koncern som är ägare av Fagerberg. Anders Andersson visade inledningsvis en bild på en 2000 år gammal ventil som finns på museum i Pompeji. Nästa ventil var från 1800-talet och fungerar nog fortfarande eller så går den att renovera. Denna typ av ventiler har uppenbarligen inte ändrats så mycket under tidernas gång. Renovering är något Fagerberg tagit fasta på. Till sin populära kulventil finns reparationssats att köpa. Under 2023 såldes 8000 satser. Därmed undveks tillverkning av 8000 nya ventiler och 108500 kg koldioxid sparades in.
– Detta är hållbarhet på riktigt. Plus att kunderna minskar sina utgifter, säger Anders Andersson.
Synd bara att inte alla kunder köper reparationssatser, till de 30000 ventiler som säljs per år.
Fagerbergs produkter består av både metalldelar och elektronik. Användaren har kanske inte tid att reparera om elektroniken fallerar, men det kan leverantören göra. I bild visades exempel där elektroniken hade bytts ut på en induktiv flödesmätare. Livslängden förlängdes denna gång med ungefär 20 år.
- När vi reparerar mätinstrument ser vi till att de inte bara klarar trycket utan också mäter rätt. Vi har tagit fram diagnostiska verktyg som säkerställer detta.
Richard Denlin menade att det som Fagerberg gör är bra, men skalan är liten. Denlin arbetar med bland annat processindustrin och där slängs enorma mängder produkter och material. Samt att det ligger en hel del på lager som aldrig kommer att säljas.
– Vi borde kunna göra mycket mer av allt detta. Problemet är också att tillverkarna slutat tillverka produkter som är möjliga att renovera. Vi som företag och även andra, bör se till att våra produkter går att renovera och laga, säger Richard Denlin.
Han tror inte att användarna ute i industrin skapar stora underhållsavdelningar för att reparera saker. Det måste kanske lösas på andra sätt, med nya affärer och helt andra samarbeten. Avslutningsvis efterlyste han samarbetspartners, bland andra industrier, helt andra aktörer som gynnar resursbesparande, eller varför inte skolor och universitet för att utveckla nya idéer.
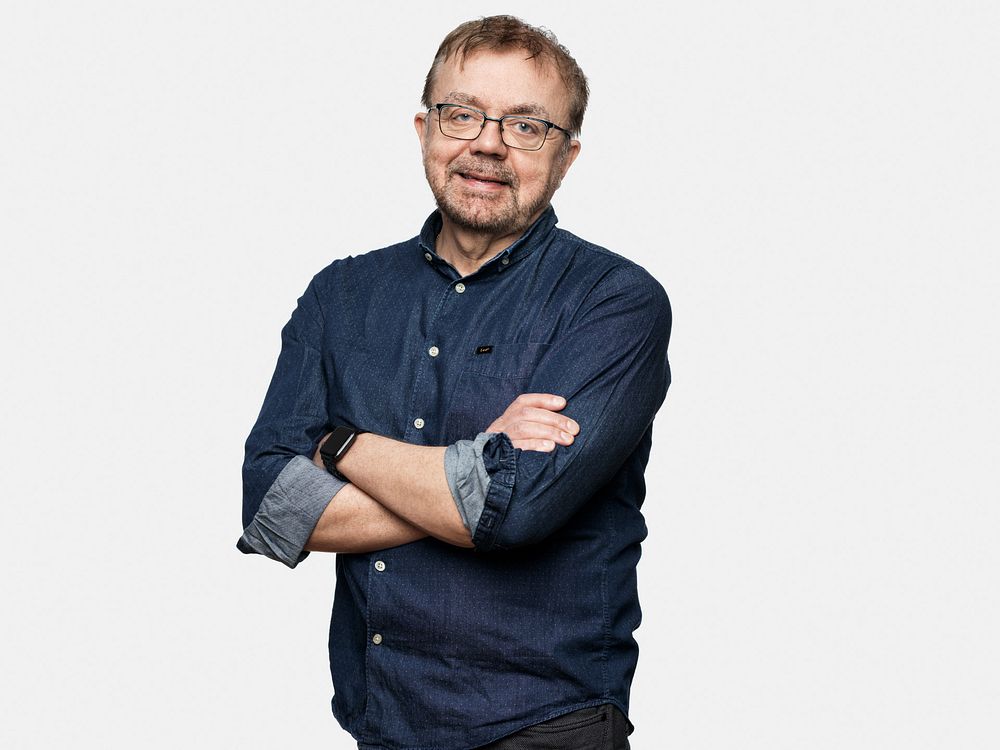
– Våra produkter består av både metalldelar och elektronik. Användaren har kanske inte tid att reparera om elektroniken fallerar, men det kan vi som leverantör göra, säger Anders Andersson från Fagerberg.
//